#FWD2022 - Q&A with Uralkali Haas F1 Chief Mechanic, Matt Scott
February 10, 2022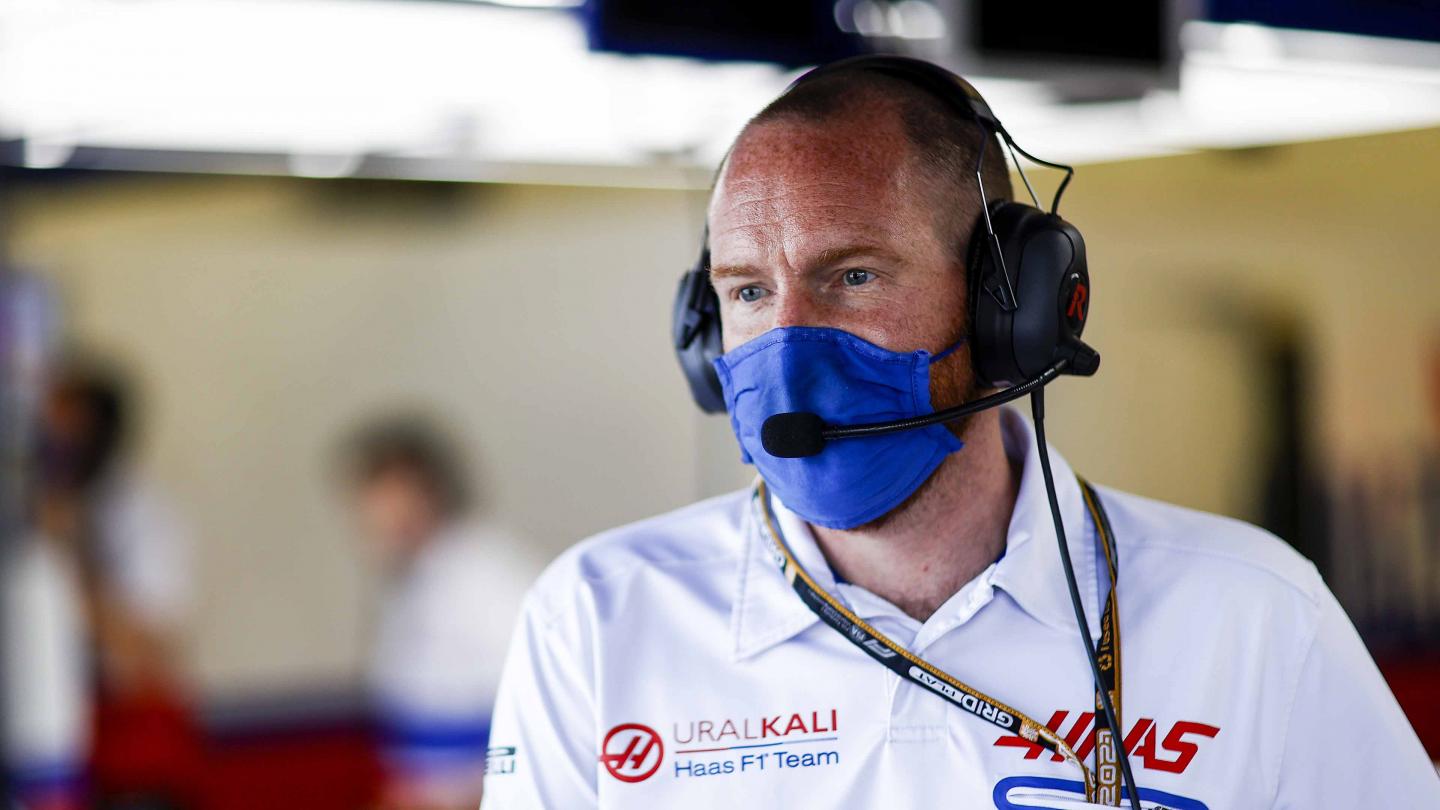
Following the digital reveal of the VF-22, Uralkali Haas F1 Team is sharing further details on its latest challenger.
Technical Director Simone Resta introduced the taskforce behind a new era of racing for America’s Formula 1 Team and the set-up of a new-look design office. As plans are manufactured into parts, Chief Mechanic Matt Scott takes over to discuss one of the most crucial times of the year – car build. He details the processes and shares the secret of exactly how many parts are used to create a Formula 1 car.
Hi Matt, thanks for taking some time to speak to us during the busiest time of the year. It’s a renowned part of the build up to a Formula 1 season, but when we say car build, what exactly does it involve?
“If you think of every Formula 1 season as a new project and at the start of that project you meet the car that the team will race and develop throughout the year. Every race week we build it, maintain it and dismantle it but the car build phase is when you take the design, make the parts, deliver them to the car build crew and hope that everything fits together.
“The car is very much a prototype, so it's not always perfect. There will be clashes, things that don't fit, things that are completely wrong, things that are really nice! It's also an important learning stage for the mechanics as they get comfortable with the car and new procedures.
“I enjoy it, some people don’t, but for me there is quite a lot of enjoyment in seeing the designs turn into an actual car in a relatively short period of time. There's nothing like it in any other industry – where you go from design release, through manufacturing, and then to driving around the circuit at 200mph within three to four weeks.”
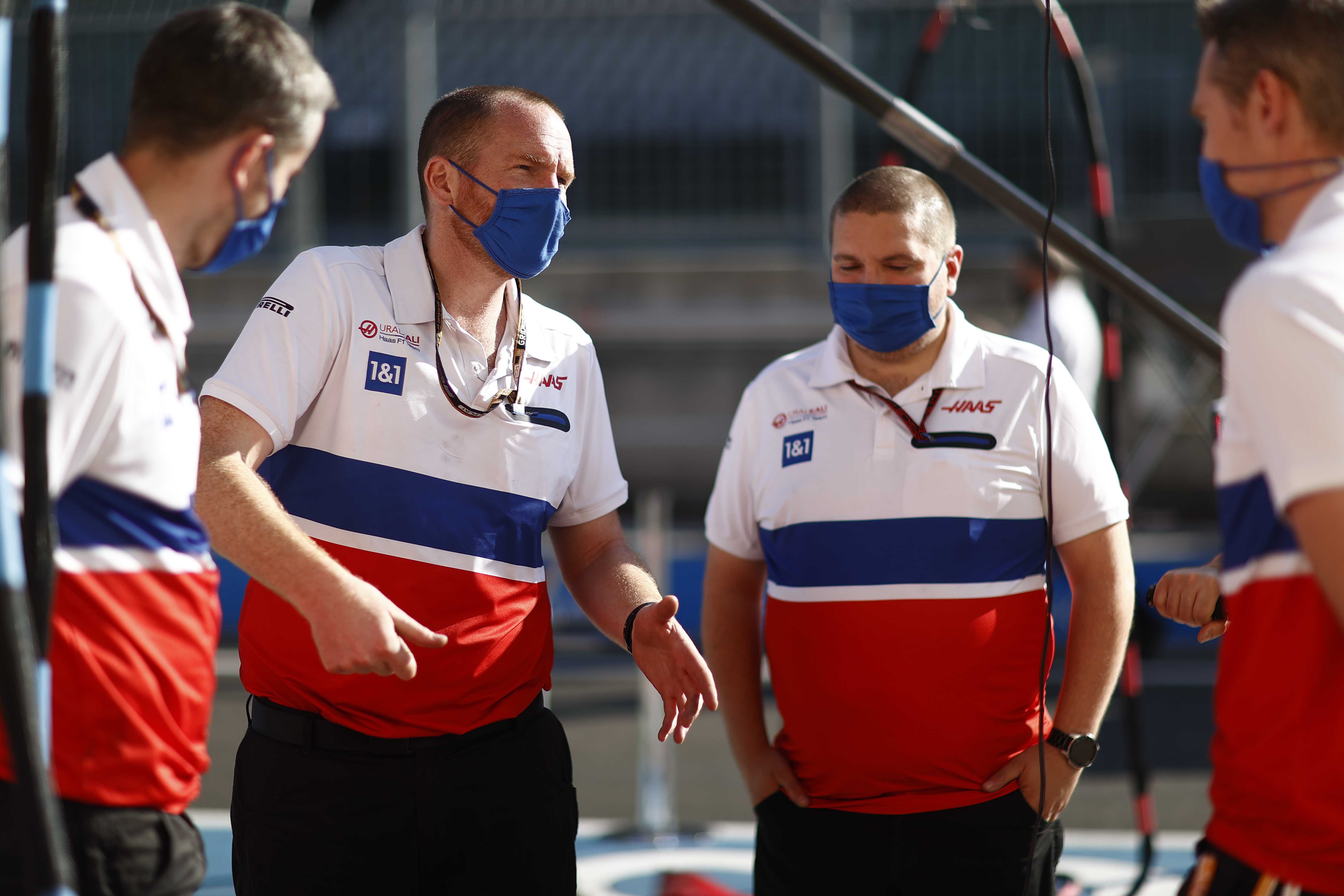
What is the objective of the car build? To literally build the car for the first time, or to check that all those parts can even make a car?
“We’re already thinking about reliability, trying to find problems, clashes, wires rubbing, not being able to get access to bolts and all other problems that can occur during this phase. Part of our job is to feed these issues back to the design team so it will get corrected down the line.
“The final part of car build is driving around the circuit, however then it starts all over again. After the first run, we take the car apart, check all the components, and put it back together although this time we know we've got all the parts.”
Is it similar to when buying from your favorite flatpack furniture store, where you get the instruction manual and it shows you step-by-step how to make it?
“A mechanic’s dream would be to have all the parts laid out like a big LEGO model with some nice, easy to follow instructions on how to build everything in an organized way. This is not the case.
“We have a schedule at the start of car build which defines when all the parts are turning up, or at least when we’d like them to turn up. Very rarely does this happen due to manufacturing times or delays in freight. It's never as easy as having all the parts turning up sequentially to suit the build.
“There's a lot of putting together and taking apart, checking, building sub-assemblies, checking again, taking apart, getting it right and then putting back together. At the start there are 3D drawings and as the weeks pass the 2D assembly drawings are released and become more and more detailed. A perfect assembly drawing is a mechanics dream!
“An added factor of our car build is that we use external vendors. We have a centralized design office, and we have key partners such as Ferrari and Dallara but from a production side we have lots of different suppliers, so each item has to be quality checked. The designer will assume that when they send their part to our purchasing team, which is then then passed on to a supplier that the part will be made to the drawing. Car build is when we find those problems. That’s when you realize there's never as much time as you want to go through all the required quality control and trial fitment stages.”
When you’re at the end of car build and some things have gone great and some things need more work on to become great, how quickly can you implement changes?
“Formula 1 is like any other motorsport; it's just the compromises are less.
“For example, you might find that you've got a pipe that’s difficult to fit but when you have the resources to fix this issue, it'll be done. However, if you've got something related to performance or critical reliability, we will do our best to fix the reliability issue within that test, and the performance issues before the first race.”
Are there troublesome areas where you can already predict time will be spent on?
“Definitely. Modern day Formula 1 cars have many complex systems, whether it's cooling, hydraulics, pneumatics, or electronics, you can expect some installation problems. We must be prepared for this. It’s a product of having a short amount of time, groups of people working on different systems and pulling it all together in a few weeks, not months, or even years that other automotive design teams might have.”
Everything we’ve discussed is standard for a regular car build but this season brings in new regulations and a dramatically new-look car. How does that change things from your perspective?
“The process is the same just with slight tweaks you have to make related to how the car is assembled. Not only for this year we have new rules but also a new design team – so the design philosophies will be slightly different – we've also got a slightly different race weekend format to plan for in 2022.
“There's been added work gone into the car to make it easier to work on and hopefully this will pay off as proposed for the new race weekend format is a reduction in working time. The theory behind the design changes will not be about the mechanics doing less on the car but making it possible for the mechanics to be able to do this work faster.”
When and where does the car build take place?
“We have a car build base at Dallara and this is the standard set-up for us. Due to COVID-19 we couldn’t do it last year but this year because Dallara are manufacturing our chassis again it makes sense to make use of their extensive modern facilities.
“To understand how long the car build takes, we factor in certain milestones. In week one, we’re getting the bare chassis and rechecking the basics - fuel cell, hard lines and then driver installation.
“That's a key factor within the car build. We can model the driver in CAD, we can transfer pedal positions across from different cars and adjust where necessary in CAD, but there's always some final tweaks. Week one and two is about work on the chassis and making sure the driver is comfortable.
“The entire process of the car build takes around four weeks and is defined by the date of the first test.”
Who exactly is involved in the car build?
“We have the program management team who coordinate ideas and using the teams’ resources turn these into parts delivered to our car build stores. Whether the parts are coming from Ferrari, from Banbury or whether the parts are coming from our base in America, they all have to meet in the car build area within a four-week window. An important part of this is process is the parts coordination team, which make sure that parts are arriving at the correct time, relaying information if they haven't to our purchasing team and organizing the parts ready for the mechanics’ requirements on a day-to-day basis.
“Once the mechanics are here, they want to build the car, that’s what they're focused on. They want to go to stores, pick up the components they need for the jobs that they've been tasked with and build the car.
“We have all mechanics here throughout the car build. For the first two weeks, we filter the mechanics to what areas they're going to work on the car. There's no point in a rear end mechanic being out when there's no rear end to work on. However, the final two weeks, we have everybody join. This isn’t just because we need people, but because everybody needs to have contact with the car before we go testing. The initial stage of testing is where the mechanics really come into their own. They're the people that spot the problems, and it wouldn’t be good practice for them to just turn up to track and expect them to be able to do their job.
“We also then have an engineering team here, which is very similar to what we have trackside regarding coordination of fault reporting. When we do find bugs from the build in the car, we can log them and get the correct people involved and react as quick as possible. If the mechanic finds an issue, rather than the part being discarded or modified ad-hoc which is potentially unrepeatable, we have a division of the engineering team to catch and sometimes literally catch, the problem and then bring the solutions.”
What’s the order of the car build?
“Once the chassis is painted, it is then all about driver fit and building the fuel cell for the final time. Next, the fuel cell and chassis ‘bolt-ons’ which include parts related to driver safety and installation. The driver installation will include steering column and driver controls. Then it's the cooling system, radiator ducts and the external parts of the chassis. Once that's done, we then move onto systems such as front suspension, brakes, and bodywork.
“Working from the rear we start at gearbox internals, rear end suspension internals and rear end suspension externals. The rear end of the car can be complete before we get the power unit. This is now when you’re coming to the end of the car build, with the big visual operations taking place – the PU, gearbox, fluid in the car, fix all the leaks and then fire up the car.
“Obviously, the installation of the engine and gearbox is a huge part of the car build, and we can't do this without assistance from Ferrari. We are a customer of theirs, but also, we require a serious amount of information to make our installation as easy as possible. They would have been working with our designers probably from the middle of last year.”
To end on a trivial note, can you share how many parts are needed to build a Formula 1 car?
“What a question to finish! Obviously, everything is very much dependent on weight. However, items must be serviceable, so you have to be able to take them apart.
“It is phenomenal how many parts there are. If you take a standard M4 bolt – a part you might have on your washing machine – we use hundreds of them in components as important as brake ducts, bodywork, to items like drivers drinks and complex heat exchangers.
“Taking a look through our bill of materials, I’d approximate around 43,000!”